A cryogenic rocket engine is a rocket engine that uses a cryogenic fuel and oxidizer; that is, both its fuel and oxidizer are gases which have been liquefied and are stored at very low temperatures. These highly efficient engines were first flown on the US Atlas-Centaur and were one of the main factors of NASA’s success in reaching the Moon by the Saturn V rocket.
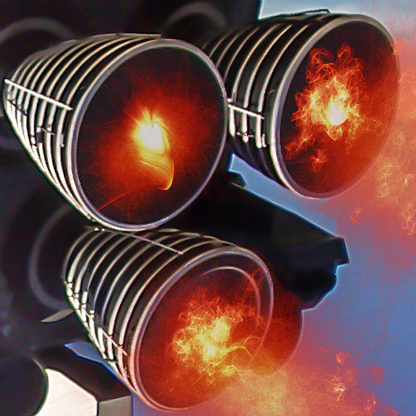
The major components of a cryogenic rocket engine are:
- Combustion chamber: This is where the fuel and oxidizer are burned to produce hot gas. The combustion chamber must be made of a material that can withstand the high temperatures and pressures of combustion.
- Pyrotechnic initiator: This is a small explosive device that is used to ignite the fuel and oxidizer.
- Fuel injector: This is a device that mixes the fuel and oxidizer in the combustion chamber.
- Fuel and oxidizer turbopumps: These pumps are used to force the fuel and oxidizer into the combustion chamber at high pressure.
- Cryo valves: These valves are used to control the flow of fuel and oxidizer into the combustion chamber.
- Regulators: These devices maintain the pressure of the fuel and oxidizer at a constant level.
- Fuel tanks: These tanks store the liquid fuel.
- Oxidizer tanks: These tanks store the liquid oxidizer.
- Rocket engine nozzle: This is a device that converts the hot gas from the combustion chamber into thrust.
In terms of feeding propellants to the combustion chamber, cryogenic rocket engines are almost exclusively pump-fed. Pump-fed engines work in a gas-generator cycle, a staged-combustion cycle, or an expander cycle.
- Gas-generator cycle: In a gas-generator cycle, a small amount of fuel and oxidizer is burned in a separate chamber to power a turbine. The turbine drives the fuel and oxidizer pumps, which then force the fuel and oxidizer into the combustion chamber.
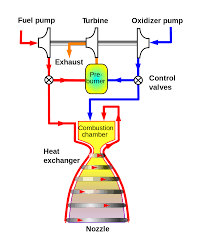
- Staged-combustion cycle: In a staged-combustion cycle, the fuel and oxidizer are burned in two stages. In the first stage, a small amount of fuel and oxidizer is burned to power a turbine. The turbine drives the fuel and oxidizer pumps, which then force the fuel and oxidizer into the second stage combustion chamber. In the second stage, the full amount of fuel and oxidizer is burned to produce thrust.
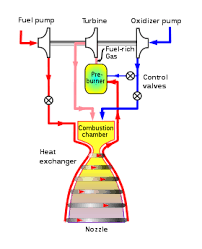
- Expander cycle: In an expander cycle, the hot gas from the combustion chamber is used to drive a turbine. The turbine drives the fuel and oxidizer pumps, which then force the fuel and oxidizer into the combustion chamber. The hot gas from the combustion chamber is then expanded through a nozzle to produce thrust.
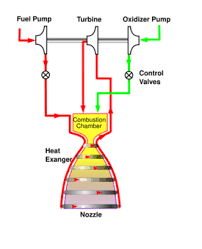
Cryogenic rocket engines are more efficient than solid rocket motors and other types of liquid rocket engines. This is because cryogenic propellants have a higher specific impulse, which is a measure of the efficiency of a rocket engine. Specific impulse is calculated by dividing the thrust of an engine by the mass flow rate of the propellants. The higher the specific impulse, the more efficient the engine.
Cryogenic rocket engines are also more complex than solid rocket motors and other types of liquid rocket engines. This is because they require cryogenic propellants to be stored and transported at very low temperatures. Cryogenic propellants are also more expensive than other types of propellants.
Despite their complexity and cost, cryogenic rocket engines are the most efficient type of rocket engine available. They are used in a variety of launch vehicles, including the Space Shuttle, the Saturn V, and the Ariane 5.
There are a number of innovations that are being developed in the field of cryogenic engines. Some of these innovations include:
- New fuel and oxidizer combinations: New fuel and oxidizer combinations are being developed that offer improved performance and efficiency. For example, liquid hydrogen and liquid oxygen are the most common cryogenic fuels and oxidizers, but they are not ideal for all applications. Newer combinations, such as liquid methane and liquid oxygen, offer better performance and efficiency at lower temperatures.
- New materials: New materials are being developed that can withstand the extreme temperatures and pressures of cryogenic engines. For example, new composites are being developed that are stronger and lighter than traditional materials, such as steel and aluminum.
- New manufacturing techniques: New manufacturing techniques are being developed that can produce cryogenic engines more efficiently and at a lower cost. For example, 3D printing is being used to create complex parts for cryogenic engines that would be difficult or impossible to manufacture using traditional methods.
These innovations are helping to make cryogenic engines more powerful, efficient, and affordable. As a result, cryogenic engines are becoming increasingly common in a variety of applications, including space launch, satellite propulsion, and air-breathing engines.
Here are some specific examples of innovations in cryogenic engines:
- In 2019, SpaceX successfully launched the Falcon Heavy rocket, which uses three cryogenic Merlin engines. The Falcon Heavy is the most powerful rocket in the world, and it is capable of carrying a payload of up to 64 metric tons into orbit.
- In 2020, NASA successfully launched the James Webb Space Telescope, which uses a cryogenic Ariane 5 rocket. The James Webb Space Telescope is the most powerful space telescope ever built, and it is designed to study the universe in infrared light.
- In 2021, Airbus announced that it is developing a new cryogenic engine for its A350 XWB airliner. The new engine is expected to be more efficient and powerful than the current engine, which will help to reduce fuel consumption and emissions.